Centrifugal Pumps Working and Applications
The first machine that was characterized into a centrifugal pump was named as mud lifting machine. This machine was appeared in the year 1475 by the Francesco di Giorgio Martini. He is an Italian Renaissance engineer. However, the actual centrifugal pumps were not implemented until the 17th century, while Denis Papin designed the pump with the help of straight vanes. In the year 1851, the British inventor namely John Appold has launched the curved vane.
The most commonly used as well as the most popular pumps are centrifugal pumps, which are mainly used for transferring the liquids. These pumps can be inbuilt with a revolving impeller for transferring water otherwise fluids with the help of centrifugal force from one place to another within several industries like municipal, plants for power generation, agriculture, industrial, chemical, mining, petroleum, pharmaceutical, etc.
What is Centrifugal Pump?
The centrifugal pump definition is, a pump which can be used for handling huge amount of liquids to provide extremely high flow rates, and they have the capability to regulate their flow of liquid rates over a wide range.
Generally, these pumps are designed for liquids which have a comparatively low viscosity that transfers like light oil otherwise water. Some of the viscosities liquids at 680F -700F will require extra horsepower to work the centrifugal pumps. Centrifugal pump components mainly include three parts such as an impeller, a casing, suction pipe by a foot valve & strainer delivery pipe.
A centrifugal pump utilizes rotation to pass on velocity in the direction of the fluid. Each centrifugal pump uses a hydraulic component like an impeller that turns to pass on velocity toward the pumped fluid.
This pump mainly used to change the velocity into liquid flow. Each pump uses a hydraulic component like a casing that captures the velocity which is informed by the impeller & directs the pushed fluid toward the pump expulsion end.
Centrifugal Pump Working Principle
The centrifugal pump working principle mainly depends on the flow of forced vortex which means whenever a certain accumulation of liquid or fluid is permitted to turn with an exterior torque than there will be an increase within rotating liquid pressure head takes place.
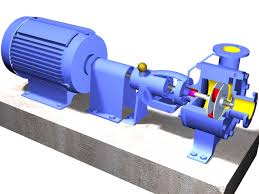
The increase in pressure head can be used to carry water from one site to another site. It is the force performing on the liquid that makes to supply in the casing.
The efficiency of Centrifugal Pump
The efficiency of a centrifugal pump can be defined as the ratio of the output power (water) to the input power (shaft). It can be demonstrated by using the following equation.
Ef = PW / PS
Where,
Ef is efficiency
Pw is the water power
Ps is the shaft power
In the U.S, the shaft power is the power given to the shaft of the pump in BHP (brake horsepower), and the water power Pw is
Pw = (Q x H) / 3960
Where ‘Q ‘is flow and ‘H’ is head.
In the above equation, the constant (3,960) changes the flow of the product & head into BHP. Above equations calculate that a pump generates 100 GPM on 30-feet of head & needs 1BHP. This will have total efficiency that is 75.7% at the end of the flow. The second equation expansion also permits the calculation of the BHP necessary at one point on the act of the centrifugal pump characteristic curve if we recognize its hydraulic efficiency.
Priming of Centrifugal Pump
The pump priming is the most important step while starting a centrifugal pump. Because these pumps are not capable of pumping vapors otherwise air. It is the one type of method where the impeller of a pump will obtain totally submerged within fluid exclusive of some air trap inside. This is particularly needed as there is a primary startup.
The priming methods are classified into four types namely manually, with a vacuum pump, with a jet pump, and with separator.
Types of Centrifugal Pump
The classification of a centrifugal pump can be done mainly based on factors like construction, design, service, application, observance with an industry standard, etc. Thus, one exact pump can fit into dissimilar groups which are discussed below. Based on the number of impellers used within the pump, these pumps are classified into the following types.
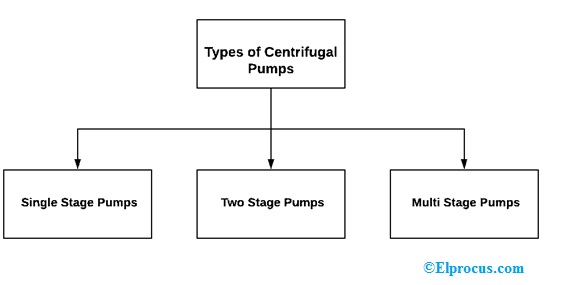
Single Stage Pump
The single stage pump is a single impeller pump, and the design and maintenance of this pump are very simple. These pumps are perfect for huge flow rates as well as low-pressure fixing. Single stage pumps are normally used in pumping services like high-flow & low to moderate total dynamic head (TDH).
Two Stage Pump
The two-stage pump can be built with two impellers which are working side by side. These pumps are mainly used in middle head applications.
Multi-Stage Pump
The multi-stage pump can be built with two or three impellers which are connected in series. These pumps are used for high head service.
Advantages of Centrifugal Pumps
The centrifugal pumps advantages include the following.
- These pumps do not include drive seals that reduce leakage risk.
- These pumps are used to pump out harmful and risky fluids.
- These pumps have magnetic coupling that can be damaged simply in overload situations as well as protects the pump from external forces.
- The motor and pump are separated from each other so heat transfer is impossible from the motor to pump.
- These pumps generate low friction.
Disadvantages of Centrifugal Pumps
The centrifugal pumps disadvantages include the following.
- The energy loss can be occurred due to the coupling that generates some magnetic resistance.
- Once the intense load occurs, possibilities are there for the coupling fall.
- If fluids with ferrous particles are pumped out, then rust occurs & over the time pump stops working.
- When the flow of liquid is less through the pump, then the overheating can occur.
Applications of Centrifugal Pumps
The centrifugal pumps applications include the following.
The centrifugal pumps are the frequently used pumps, and the flow of fluid makes them useful in several applications like industries, pressure boosting, water supplying, domestic necessities, support fire defense systems, regulating boiler water, and sewage drainage, etc. Some of the major applications include the following.
- These pumps are used in the oil and energy industries for pumping oil, mud, slurry, and power generation plants.
- These pumps are used in industrial and fire protection for ventilation & heating, boiler feed, pressure boosting, fire security sprinkler systems, and air conditioning.
- These pumps are used in waste management, agriculture, and manufacturing for wastewater processing plants, gas processing, irrigation, drainage, municipal industry, and overflow security.
- These pumps are used in food, chemical, pharmaceutical industries for hydrocarbons, paints, cellulose, petrochemical, beverage production, sugar refining, and food.
Thus, this is all about centrifugal pumps which operate through the transmission of rotational energy from several impellers. When the act of the impeller enhances the velocity and pressure of liquid then it directs it in the direction of the outlet of the pump. By its easy design, the pump operation & maintenance can be simple and well understood. Here is a question for you, what is the specific speed of the centrifugal pump?